Лазерная резка произвела революцию в промышленном производстве с момента своего появления в 1970-х годах. Сегодня она широко используется для обработки различных материалов, таких как листовой металл, пластик, стекло, керамика, полупроводники, текстиль, дерево и бумага. С развитием технологий лазерная резка будет занимать всё более важную роль в точном и микромеханическом производстве. Её универсальность и расширяющиеся возможности гарантируют, что она останется незаменимым инструментом для множества отраслей.
Что такое лазерная резка?
Лазерная резка направляет мощный лазерный луч на заготовку, где интенсивное тепло быстро плавит или испаряет материал. Когда лазер движется вдоль контуров дизайна, материал продолжает плавиться. Газовый поток удаляет расплавленный материал с реза, оставляя узкий зазор, почти равный ширине сфокусированного лазерного луча. Этот процесс позволяет получить чистые и точные резы с минимальными потерями материала, что делает лазерную резку одним из самых эффективных методов обработки различных материалов. Кроме того, лазерная резка позволяет создавать сложные и детализированные формы, которые невозможно выполнить с помощью традиционных методов резки.
Процессы лазерной резки
Лазерная резка не ограничивается только стандартным процессом. Существуют специализированные методы, такие как плазмассистированная резка и газификационная резка, которые дают дополнительные преимущества в определённых приложениях. Например, плазмассистированная резка использует плазменное облако, состоящее из ионизированного металла и газа для резки, чтобы улучшить процесс. Это облако поглощает энергию от CO2-лазера и передает её непосредственно на материал, ускоряя резку и повышая эффективность. Однако плазмассистированную резку можно проводить только с использованием CO2-лазеров, так как плазменное облако пропускает свет от твёрдых лазеров.
Газификационная резка, в свою очередь, направлена на испарение материала, а не на его плавление, что снижает тепловое воздействие на окружающие области. Этот метод идеально подходит для обработки немелящихся материалов, таких как тонкие пластиковые пленки, древесина, бумага и поролон. Появление ультракоротких импульсных лазеров, таких как пикосекундные лазеры, расширило применение газификационной резки, позволяя обрабатывать более широкий спектр материалов. Этот метод позволяет получать чистые резы без образования заусенцев и термических повреждений.
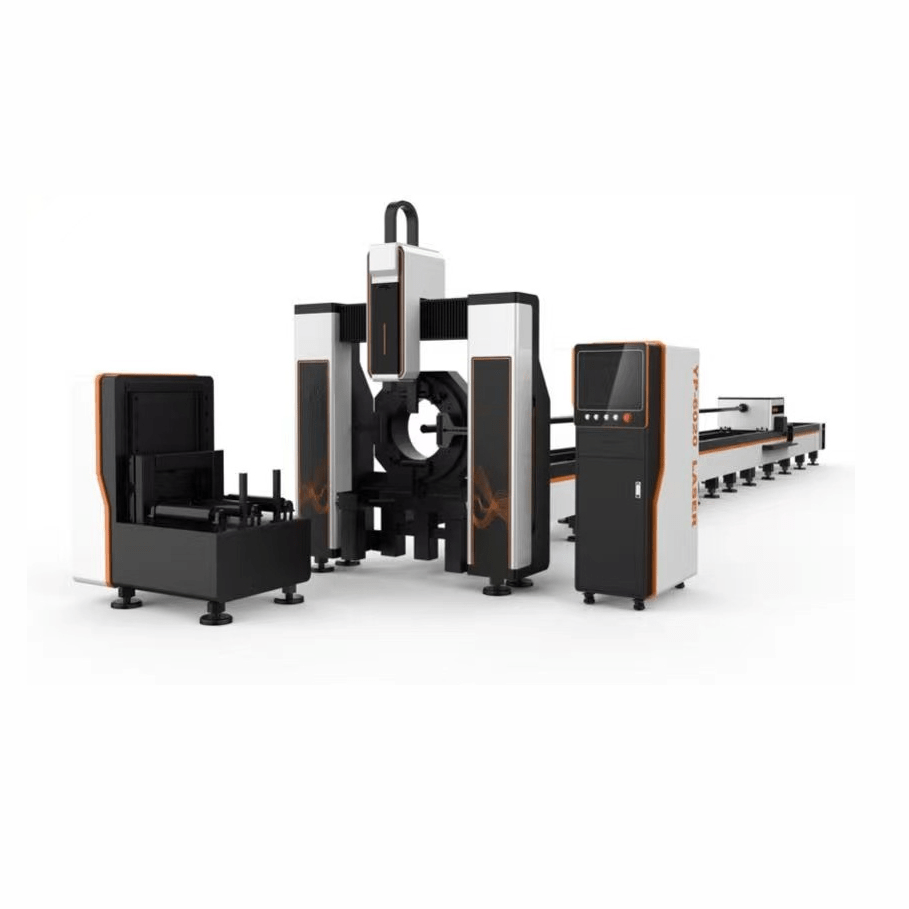
Влияние чистоты и давления газа
Чистота и давление газа существенно влияют на эффективность лазерной резки. Для резки часто используют кислород и азот, но каждый из них требует определённого уровня чистоты для достижения оптимальных результатов. Например, для резки кислородом чистота газа должна составлять не менее 99,95% для получения точных резов. Для резки азотом необходима ещё большая чистота — 99,995% или даже 99,999% — а также более высокое давление для эффективной резки более толстых материалов. Правильное сочетание чистоты газа и давления способствует более быстрой резке, лучшему качеству кромок и общей эффективности процесса.
Упрощенные настройки для операторов
Ранее операторы вручную регулировали настройки с помощью метода проб и ошибок, что занимало много времени и было подвержено ошибкам. Сегодня современные системы управления хранят заранее запрограммированные настройки для различных материалов и толщин. Операторы могут выбрать нужные параметры всего несколькими кликами, что снижает вероятность ошибок и повышает производительность. Эта технология позволяет даже новичкам достигать высококачественных результатов. Использование предустановленных параметров помогает упростить процессы, сэкономить время и минимизировать риск ошибок.
Оценка качества лазерной резки
Для оценки качества лазерных резов необходимо учитывать несколько факторов. Видимые дефекты, такие как образование заусенцев, вмятины и шероховатости, легко заметить невооружённым глазом. Однако для точной оценки таких характеристик, как вертикальность, шероховатость и ширина реза, требуются специализированные инструменты. Кроме того, важно учитывать другие факторы качества, такие как осаждение материала, зоны термического влияния и деформация, которые могут повлиять на долговечность и целостность материала. Оценка всех этих факторов гарантирует, что процесс лазерной резки не только точен, но и обеспечивает долговечность изделий.
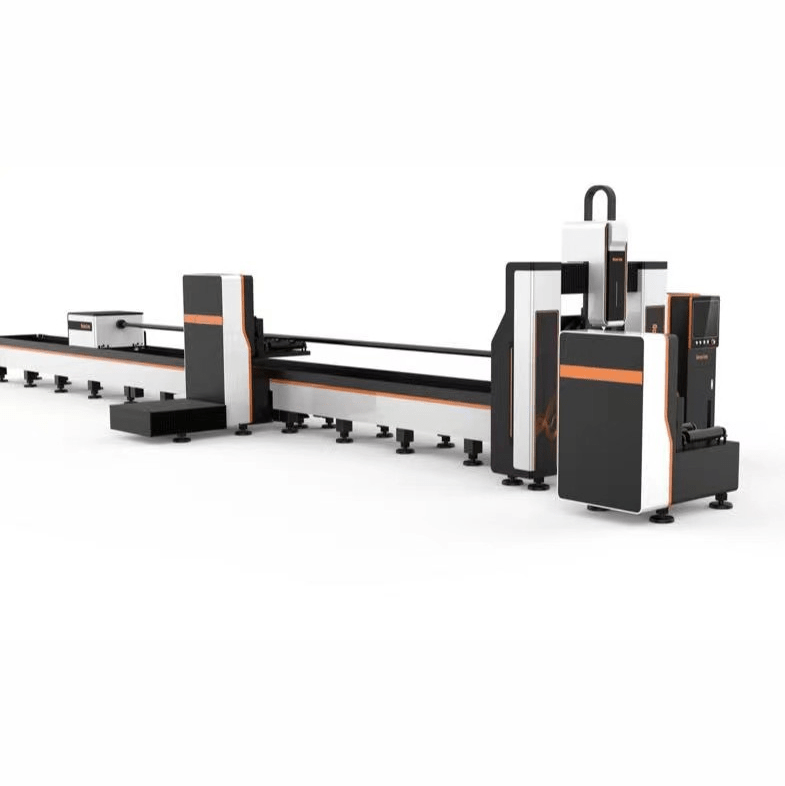
Будущее лазерной резки
Будущее лазерной резки выглядит многообещающе, так как технология продолжает развиваться и расширять область применения. С ростом спроса на точное производство лазерная резка играет всё более важную роль в таких областях, как микромеханика и высокоточное промышленное производство. Благодаря своей скорости, точности и универсальности лазерная резка стала незаменимым инструментом в современном производстве. С появлением новых инноваций лазерная резка будет продолжать двигать прогресс, улучшать производственные возможности и помогать предприятиям оставаться конкурентоспособными.